Continuous Improvement Coordinator
Hammond Power Solutions
Date: 12 hours ago
City: Guelph, Ontario
Contract type: Full time
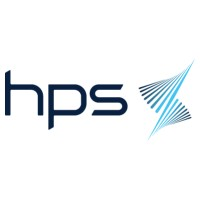
Hammond Power Solutions Inc. is a global manufacturer headquartered in Guelph, Ontario, Canada. HPS has grown to become the leader in North America in the custom design and manufacture of dry type transformers. For the past century, HPS has grown to deliver electrical power solutions to global markets and provides solutions for complex applications like, mining, rectifier, drives, traction, wind, solar and many other electrical power applications. The world relies on HPS to continually conceive and produce state-of-the-art transformer technology. We currently have an opening for a Continuous Improvement (CI) Coordinator -come grow with us!
In this role, we are looking for the successful candidate to apply the lean manufacturing tools necessary to ensure compliance with plant metrics and ensure processes run efficiently and effectively. The candidate will also define and implement mechanisms necessary to identify and manage process improvement initiatives in our Guelph manufacturing facility. This role reports to the Plant Manager of the Guelph location.
Key Responsibilities
Project Development and Implementation:
Education and Training:
In this role, we are looking for the successful candidate to apply the lean manufacturing tools necessary to ensure compliance with plant metrics and ensure processes run efficiently and effectively. The candidate will also define and implement mechanisms necessary to identify and manage process improvement initiatives in our Guelph manufacturing facility. This role reports to the Plant Manager of the Guelph location.
Key Responsibilities
Project Development and Implementation:
- Implementation of Continuous Improvement projects and derivatives of the Ideas Program.
- Analysis of each idea together with the departments involved.
- Follow-up of the implementation of each approved idea and the needs.
- Develop, maintain and update the standard practices (SPI's) of the methods involved.
- Prepare the necessary documents that guarantee the sustainability of the implemented projects.
- Keep the program recognition system up to date in SharePoint and provide feedback to the staff participating in the program.
- Ensure the replication of the ideas that apply in other areas of the plant.
- Manage the stock of souvenirs of the ideas program.
- Implement the foundation, employee involvement, 5's and analysis and problem-solving.
- Red zone administration for the 5's program.
- Follow-up of findings in 5's audits.
- Stock management of items required for maintenance of 5's in the plant.
- Coordinate recognitions to continuous improvement teams.
- Update weekly and monthly indicators of the teams.
- Collaborate in activities of other departments.
- Preparation of presentations for the teams.
Education and Training:
- College Diploma or University Degree in Industrial, Mechanical or Electrical Engineering preferred or equivalent experience.
- Proven hands-on leadership and problem-solving skills in a team-oriented, cross-functional environment.
- Excellent communication skills and a high level of enthusiasm and a passion for change.
- Willing to accommodate production needs with work schedule when required.
- Self-starter and results driven.
- Strong interpersonal skills.
- Computer skills including, Word, Power point and Excel.
- Effective working in a team environment.
- Strong project management skills are an asset.
- Strong working knowledge of Lean Manufacturing principles.
- Six Sigma Certification is an asset.
- Excellent trouble-shooting and analytical skills.
- Minimum 2 - 5 years practical experience regarding lean manufacturing principles, understanding & implementation.
- Minimum 2 - 5 years manufacturing supervision or manufacturing engineering background.
- Minimum 2-5 years hands on experience in a manufacturing sector.
See more jobs in Guelph, ON